Ceramic foam filter is just developed as a new type of molten metal filters to decrease casting flaw recently. It is made from high quality ceramic materials, whose main components are Al2O3, Sic, ZrO2, MgO etc. Ceramic Foam Filter has the characters of light weight, high mechanical strength, large specific surface areas, high porosity, excellent thermal shock resistance, chemical corrosion resistance and high temperature stability in molten metal. With the distributing pores net structure, they are able to increase the surface areas, and absorb the sinter, the liquid metal becomes more pure, waster quality problems such as sand pore and air pore are much less and the cast quality becomes much better.
Classification and Specifications:
*Alumina / Al2O3 Ceramic Foam Filter
It's mainly for filtration of aluminum and aluminum alloys in foundries
*Zirconia / ZrO2 Ceramic Foam Filter
It's used for molten all types of steels like unalloyed, low alloyed, stainless and high-alloyed as well as Nickel and Cobalt-based super-alloys
*Silicon Carbide/SiC Ceramic Foam Filter
It's mainly for filtration of cast iron (grey iron & ductile iron) and non-ferrous alloys
Advantages:
*High porosity
*Low loss of thermal shock
*High mechanical strength at normal and high temperature
*Large specific surface
*Good chemical stability
*Excellent filtering functions of screen
*Excellent filtering residua collection and absorption
Type | Alumina CFF | Silicon carbide CFF | Zirconia CFF | Magnesia CFF |
Material | Al2O3 | Sic | ZrO2 | MgO |
Applied temperature | ≤1200celsius degree | ≤1500celsius degree | ≤1700celsius degree | ≤1100celsius degree |
Color | White | Grey black | Yellow | Yellow |
Bulk Density | 0.35~0.55g/cm3 | 0.45~0.65g/cm3 | 1~1.5g/cm3 | 0.5~0.7g/cm3 |
Bore Density | 10~60PPI | 10~60PPI | 10~60PPI | 10-60ppi |
Porosity | 80~90% | 80~90% | 80~90% | 80-90% |
Bending Strength | 0.6Mpa | 0.8Mpa | 0.8-1.0Mpa | 0.6Mpa |
Compression Strength | ≥0.8Mpa | ≥1.0Mpa | ≥1.5Mpa | ≥0.8Mpa |
Thermal Shock Resistance (1100celsius degree ~ Room Temperature) | Not break after 6 times thermal shock testing | |||
Application | Molten Aluminum and Alloy | Molten Iron and Alloy | Molten Stainless Steel, Alloy and other metal in precision molding | Molten magnesium and its alloys |
Square (mm) | Maximum filtration capacity (kg) | Normal flow rate of liquid metal (kg/s | Circular (mm)) | Maximum filtration capacity (kg) | Normal flow rate of liquid metal (kg/s | ||||
Ductile iron | Gray iron, copper and aluminum castings | Ductile iron | Gray iron, copper and aluminum castings | Ductile iron | Gray iron, copper and aluminum castings | Ductile iron | Gray iron, copper and aluminum castings | ||
40*40*22 | 32 | 64 | 3 | 4 | Φ40*22 | 25 | 50 | 2 | 3.5 |
50*50*22 | 50 | 100 | 4 | 6 | Φ50*22 | 35 | 70 | 3 | 4.5 |
60*60*22 | 72 | 144 | 5 | 8 | Φ60*22 | 50 | 100 | 4.2 | 6.5 |
75*50*22 | 75 | 150 | 6 | 9 | Φ70*22 | 75 | 150 | 5.5 | 8.8 |
100*50*22 | 100 | 200 | 8 | 12 | Φ80*22 | 100 | 200 | 7.2 | 11 |
75*75*22 | 110 | 220 | 9 | 14 | Φ90*22 | 120 | 240 | 9 | 14 |
80*80*22 | 150 | 300 | 12 | 18 | Φ100*22 | 140 | 280 | 11 | 17 |
100*100*22 | 200 | 400 | 16 | 24 | Φ110*22 | 190 | 380 | 13 | 20 |
150*100*22 | 300 | 600 | 24 | 36 | Φ120*22 | 230 | 460 | 16 | 25 |
150*150*22 | 450 | 900 | 36 | 54 | Φ150*22 | 350 | 700 | 25 | 30 |
,
Riding position
Foam ceramic filters can be placed in all parts of the gating system, should be selected according
to the characteristics of castings and production conditions, as close as possible to the casting to
achieve the best filtering effect. In practical application, according to different castings and
requirements, The following could be done: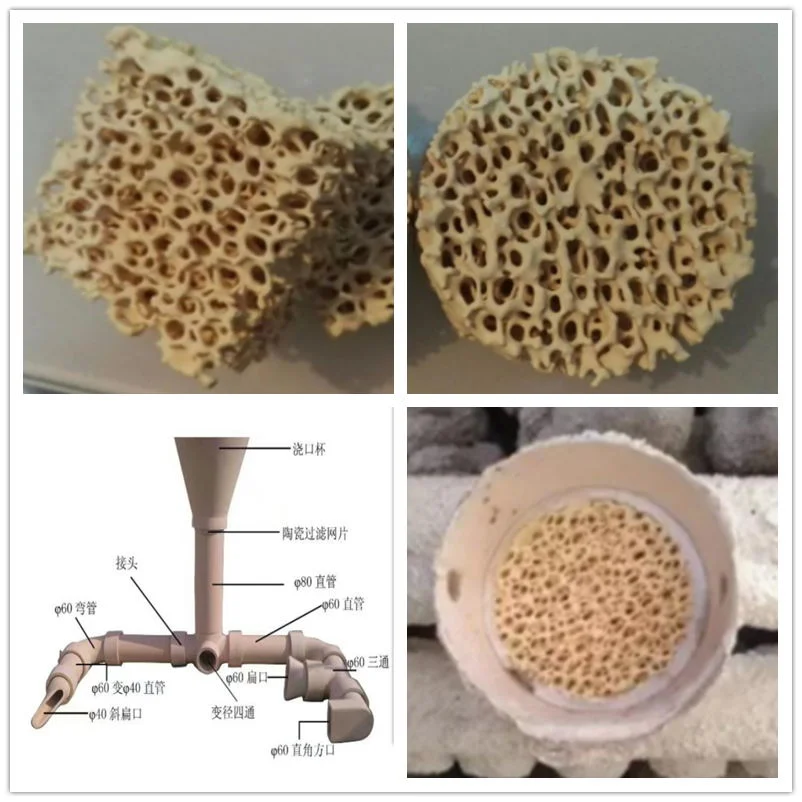
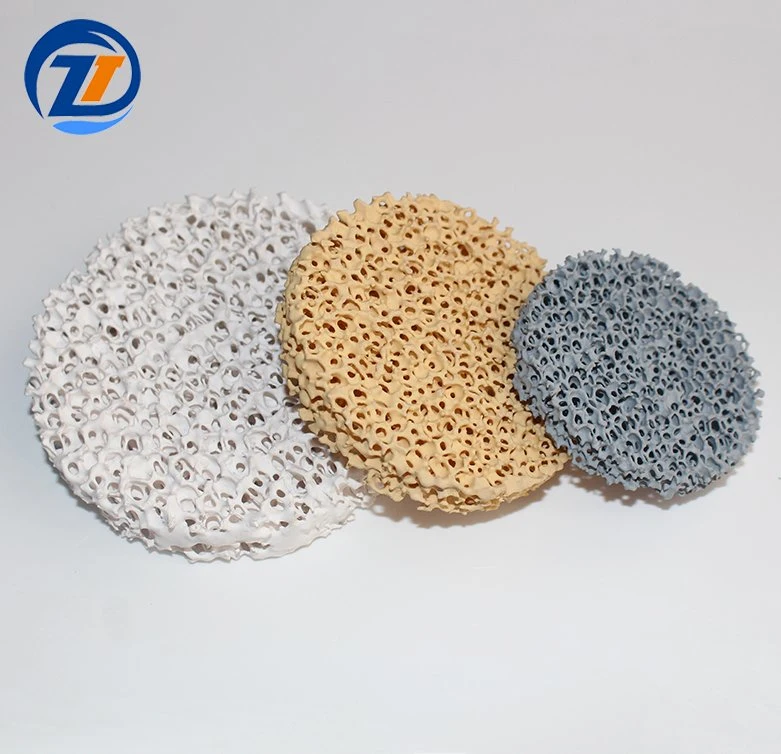
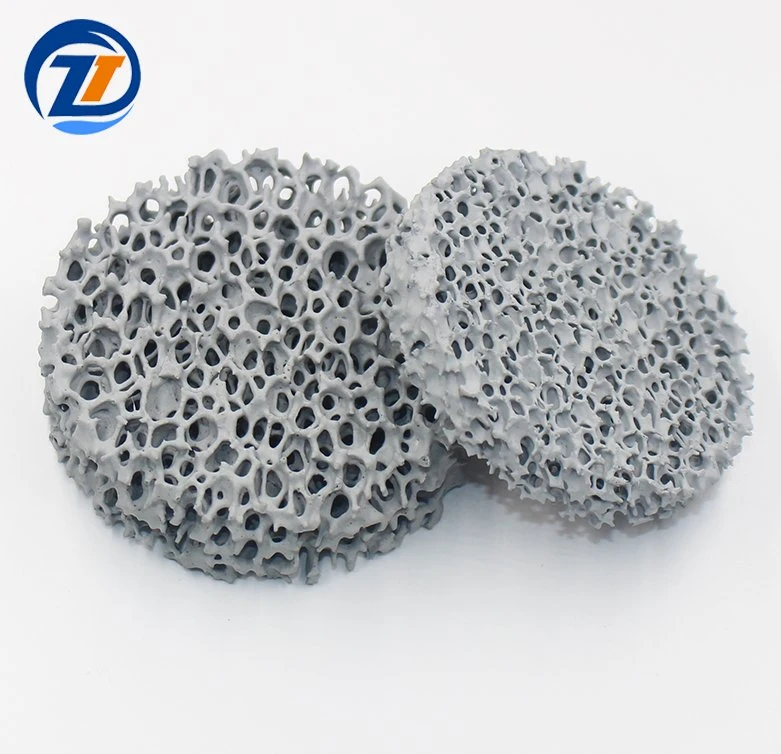
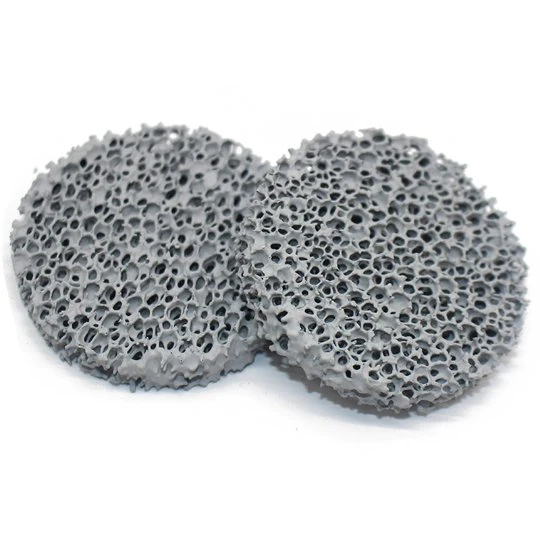
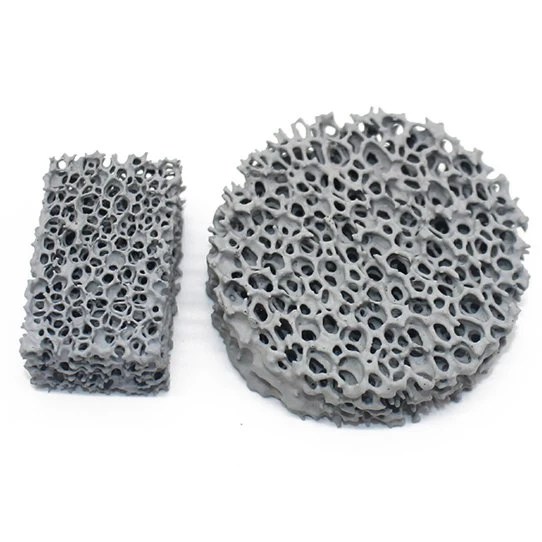
PACKAGE
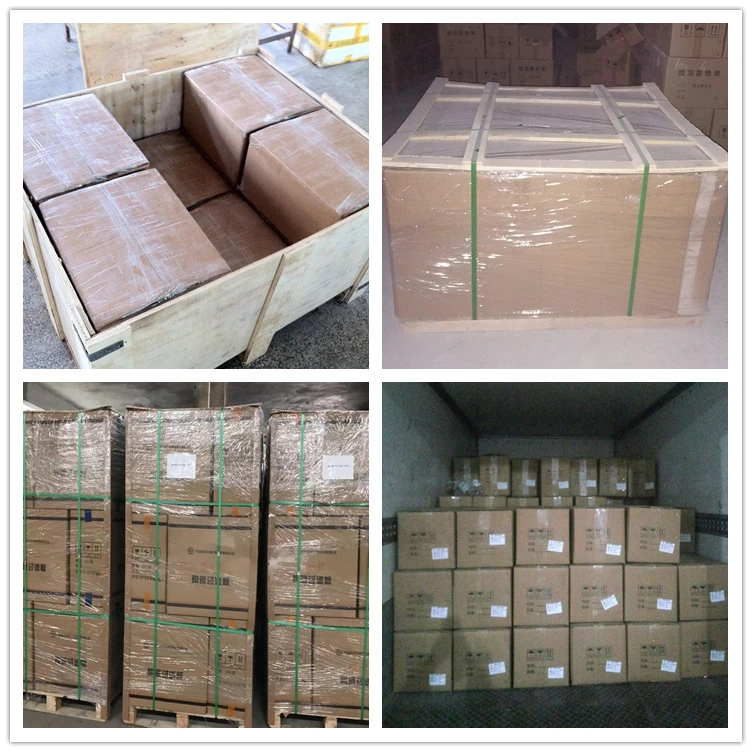
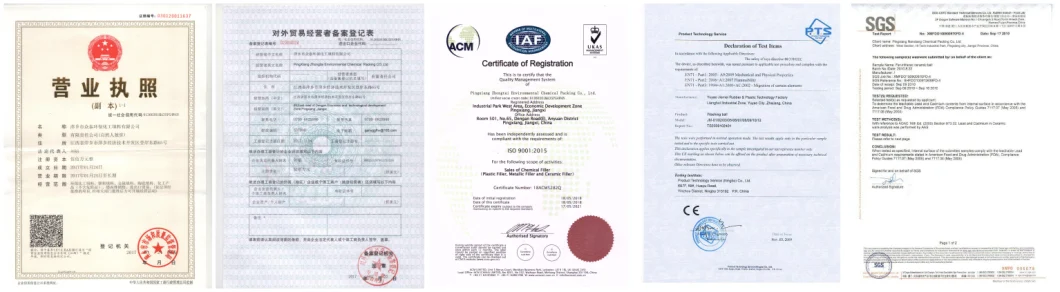
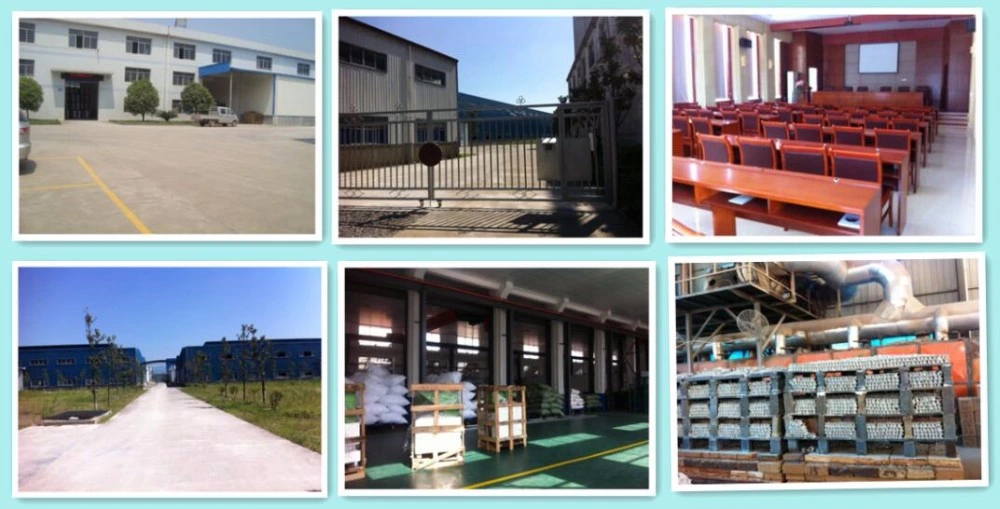